Essex Retrofit - Revisited
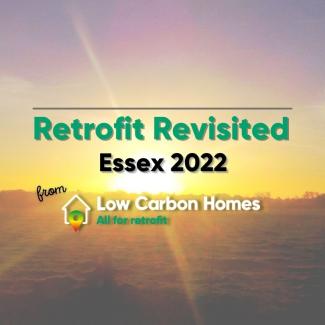
“I’m here at the county hospital site in Colchester, standing backed by the archaeological investigations which are producing innumerable, wonderful finds, including glassware with gladiators carved on it and pottery,” Councillor Lesley Wagland, Deputy Leader and Cabinet Member for Community, Equality, Partnerships and Performance at Essex County Council told Essex Retrofit Summit attendees, as she highlighted some of the fascinating finds at a site on which Essex Housing would soon build green homes.
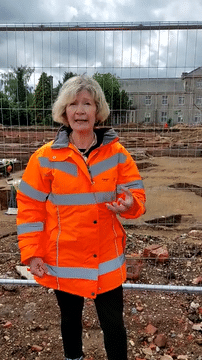
“Neutral carbon is something that’s very close to our hearts here at Essex County Council,” Lesley continued. “We’ve been hugely supportive of the development of skills and green tech, and have been part of the five sectors we’ve identified as part of our sector growth paper.
Loretta Hoy, Green Sector Developmental Lead at the Council, expanded on her colleague’s comments, telling us how the Council was facilitating wider decarbonisation opportunities for Essex businesses and communities — a key theme of our conference.
“We’ve been working on a strategy for the last eighteen months called the Sector Development Strategy which is looking at the sectors of the future which have the greatest opportunity for growth within the county.
The strategy, Loretta told attendees, identifies retrofit as a key sector with huge growth potential. “Construction and retrofit will probably be one of the largest and most important of our sectors in terms of GVA and job growth potential.
This also presented a huge challenge, she explained. “We’ve got about 650,000 homes. Every one of those is going to have to become more energy efficient and we know that we’re going to need at least 10,000 jobs in the construction trades in order to make that happen. We’ve got a big job to do as a council, a county and a community.”
The gift of employers
Many of our speakers highlighted the huge potential for job growth in retrofit in Essex. “Retrofit Academy figures show that Essex will need 7,308 tradespeople, 3,271 retrofit advisors, 1,636 retrofit assessors, 1,178 retrofit coordinators and 491 retrofit evaluators and 164 designers”, Loretta highlighted, so 14,048 people altogether, to meet its carbon neutrality targets, Loretta informed us.
This also presents a challenge of attracting new entrants to retrofit, a question our panel wrestled with during one of our Q&A sessions.
“What it does need is employer engagement,” Celine McGeown, Customer Engagement Manager, CITB (South East), contended. “The sort of thing we’re thinking of doing with industry is running things like taster days with young people.
“We’ve heard that 40% of young people that are doing a construction course in a further education or school environment don’t go into the construction industry,” Celine pointed out. “We’ve got this huge disparity between people who’ve shown an interest but don’t find or take those opportunities to progress their career. We introduced a platform last year called Talentview. Construction-specific platform for new entrants into the industry. You can search in your local area and get people talking.
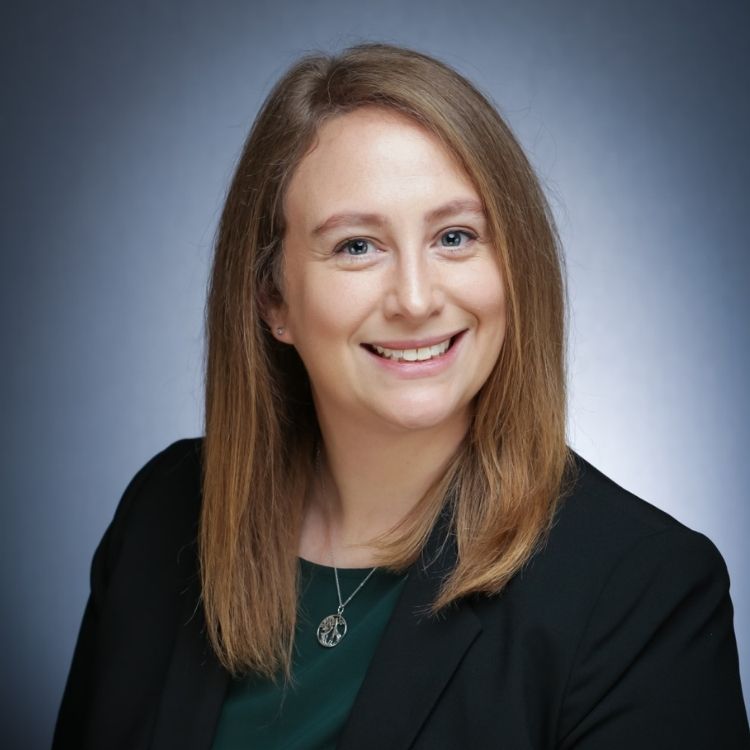
Loretta emphasised the importance of articulating to young people the variety of work on offer. “We’ve got white collar occupations as well as blue collar. It’s really important for us to be able to articulate that. Obviously the sectors you’ll have seen before are predominantly gender-biassed towards men too. We’ve got a huge job to articulate that market to the future workforce — millennials and Gen Zers for example — and how we can potentially diversify the workforce.”
Jenny Pierpoint, Chief Operating Officer (COO) at the Retrofit Academy, agreed with Loretta that the local supply chain wasn’t mature enough yet to carry out all of the county’s retrofit projects. But she also outlined what the Academy was doing to combat that such as the Harlow and Tendering Retrofit Pipeline for Economic Renewal project.
“We’re working with the Council’s Adult and Community Learning Team to set up a training provider in Essex,” Jenny said. “In addition, we’ve set up a large-scale PAS 2035 upskilling programme for over 200 fully-funded learners. I’d particularly like to highlight that we still have 60 of 100 places available for the NOCN Level 2 Award in Understanding Domestic Retrofit qualification.”
Genevieve Dady, Supply Chain Engagement Officer, South East Net Zero Hub, speaking at the Q&A, called on contractors to take on more apprentices. “It really is in the gift of employers. I know it’s a big ask bringing in apprentices and offering work experience. But it does give them that opportunity.”
But it didn’t need to be young people entering the workforce, Genevieve pointed out. “It could be people who want to change careers; there may be engineers who want to move into retrofit. In terms of retrofit coordinators or advisors, we get a number of those who’ve come from other industries because they see there’s a market for it or because they want to do their bit for the environment.
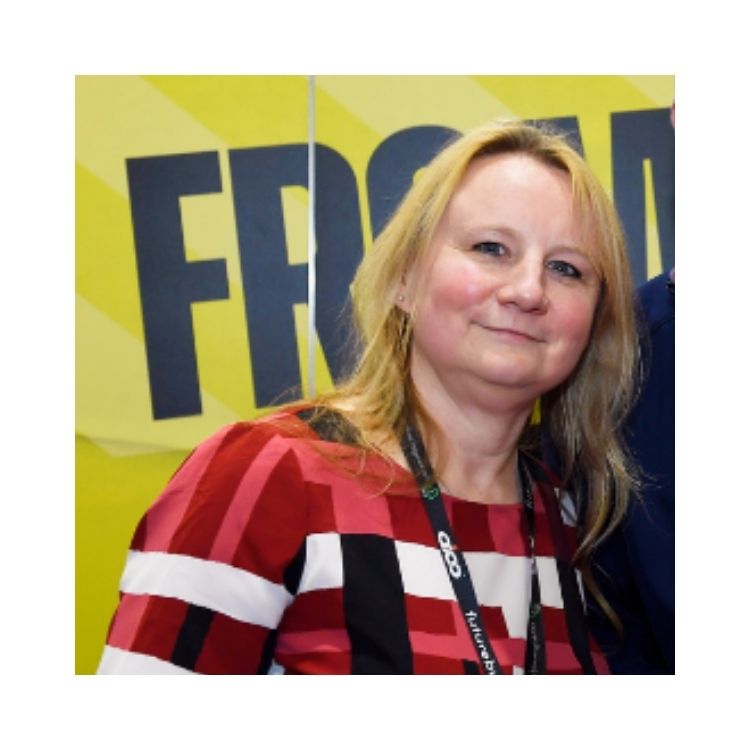
“There’s also the Green Skills Bootcamps coming up as well. There’s lots of different routes in and I recommend people get in touch with the Construction Leadership Council and the CITB.”
Donna Williams, Group Director of Sustainability & Climate Change at Sanctuary Housing stressed that there’d be opportunities for established construction workers to reskill as well. “Many organisations like us have a large pool of maintenance workers like gas engineers that will all need to be retrained to install the new techs, and there’s a real mixture of the quality of the data we have for informing these retrofit plans.
Donna also pointed out that there was a consensus emerging in housing policy making circles that the social housing sector would be the key site for growing retrofit projects. “The sector can act as a testbed for scaling up retrofit and can enable supply chains to come together.”
Tony Crawley, Chief Executive of Zenova, offered insights on what was holding back retrofit in the social housing sector and what his company’s new products were doing to change that.
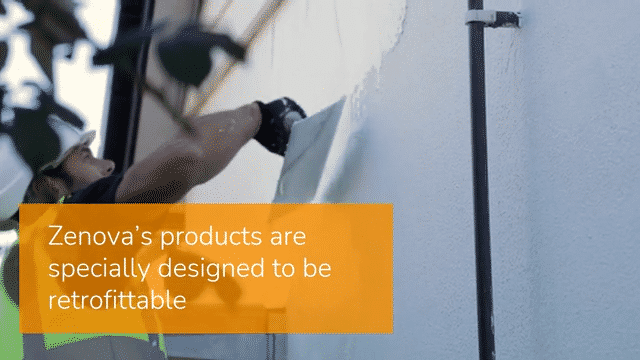
“The key issue is cost. Adding insulation is seen to be very expensive. But the challenge is greater for social housing providers: one council recently spent £2.5m making the 75 flats of an estate more energy efficient. This included upgrading double glazing as well as insulating the entire block. However, at £33,000 a piece, that council estimated it would cost £125m to bring 5,000 homes up to that standard.
“It’s a result of the current approach to retrofitting and insulation which relies heavily on the use of existing insulation techniques such as mineral board, insulation board and cladding which don’t lend themselves to retrofit as they’re costly, labour-intensive, time consuming, disruptive, and take up indoor space.
Zenova had developed best-in-class insulation products which were changing the way buildings are insulated, Tony said during his presentation. “Our products create a thermal barrier which when applied to properties stops heat escaping or entering it. Zenova products are easy to apply to external and internal walls, and provide a superb finish. Finally, they significantly improve properties’ EPC rating whilst providing a decorative upgrade and improved fire rating.”
Tony was also on hand to answer attendees’ questions about this new, unique product. “The products are vapour permeable and breathable, so we don’t get any condensation build-up on the products,” he explained. In addition, Zenova’s insulation products improve buildings’ fire ratings. “These products have been designed and brought to market bearing in mind the new building regs. They’re fire tested with Warrington Fire to meet the EN13501-1 fire rating, which is flame spread basically. So we’re improving the internal decoration fire performance.”
They couldn’t even hear it running
“Social housing providers and developers need to find low-cost, highly efficient electric heating systems for their properties to meet government sustainability targets,” Oliver Baker, Managing Director at Ambion Heating, said during his presentation.
This would require a choice of innovative technologies such as Ambion’s computer-controlled infrared (CCIR) heating system and the KERS renewable water heating system. These were, Oliver said, the ideal alternative to high temperature heating systems, as an all-electric system with exceptional levels of energy performance.
“It’s as easy to install as a conventional panel heating system, versatile enough to suit different properties and typically comes with lower costs: up-front costs decrease by 57% and lifetime costs by 35% (versus an air source heat pump in a two bedroom house), meaning social housing providers can boost their stock’s energy performance on a budget while delivering affordable warmth.”
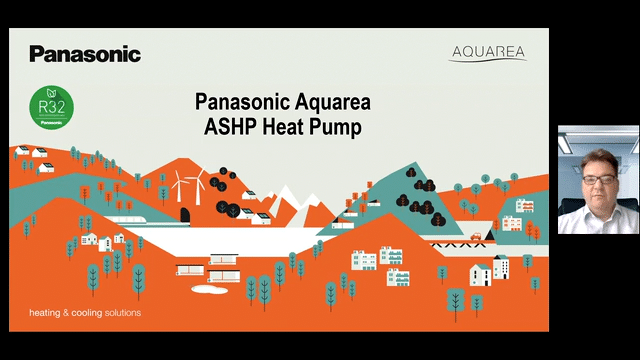
Sean Graham, Area Sales Manager at Panasonic UK, tackled some common misconceptions around heat pump technology. “We all think of heat pumps as being quite new. We actually started manufacturing them in 1973, so it’s not new technology. In fact, everyone here today will have a heat pump in their house in the form of a fridge which works in reverse.”
Sean also tackled the notion that heat pumps were noisy. “It’s a question we get asked a hell of a lot to be honest. We had a roadshow in Basildon and most of the tenants that came up to us to look at the equipment were asking about noise. A lot of them were asking if you could hear it running — it was running while we were speaking! They couldn’t even hear it running.”
And had there been a rush of enthusiasm for the BUS, one attendee asked him during the Q&A. “Other schemes have come and gone — the Domestic Renewable Heat Incentive, the Green Homes Grant — and I’ve not seen this kind of buzz before. I’ve seen heating guys who have never done a heat pump before ringing us up wanting to chat, wanting training because of the BUS.”
Iain Carr, Director of Domestic Sales at ground source heat pump manufacturer Kensa Contracting, also had some thoughts on the BUS. “It’s a bit of a tricky one still. Because of other funding opportunities that share ground source systems you can’t always use both.
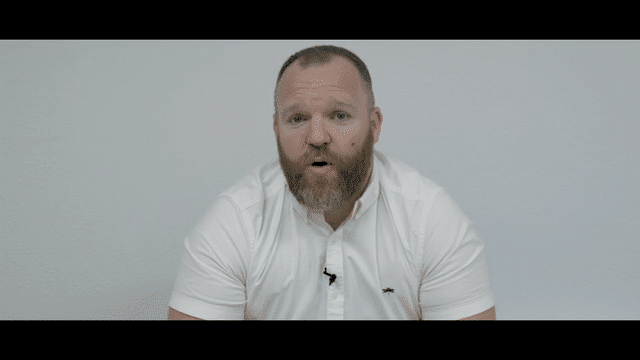
“But if it’s privately funded infrastructure, which we’re heading towards with the Kensa utilities model, where it invests in the infrastructure and then charges an annual standing charge like the gas network does, then that’s completely funded by someone else, and then the BUS can be used for the heat pump by the individual. So it’s not ruled out but it depends on what the wider scheme looks like. So yes and no!”
It was a classic case of economies of scale encouraging a community approach to retrofit projects, we discovered. “Essentially, the scale of the Kensa solution could be anything as small as two properties, with one borehole serving energy supply to both homes. The only difference is there’s a higher capital cost.
“It’s perfectly feasible. But because we’re mostly about large-scale deployment, we look to partner with other organisations where there might be two on one street and then five on the street after that. And then we minimise all of those initial capital costs by spreading it across larger scale projects.”
Community energy retrofit is happening!
“We’re part of a wider UK network,” Esmé Donghi, Project Director at Community Energy South told attendees. “There are 424 community energy schemes in 2020 working on a range of projects, including 132 working on energy efficiency, or retrofit-related projects.” It was refreshing to hear just how widespread community energy groups had become nationally.
Esmé told us more about what CES does. “We work with a range of local authorities including Surrey County Council, Hampshire, Essex and South Downs National Park. We essentially look to focus on net zero strategies within local authorities and support their implementation at a local level. And we help local communities build self-sustaining businesses. “We do this by acting as a support mechanism and we focus on training, mentoring, providing tools and resources to community groups.”
“Community energy retrofit is happening! Community energy organisations are well placed to deliver retrofit projects. They’re a ground level resource for retrofit. The shift is changing from community-owned renewable energy to other EE projects, outreach and engagement.
“Energy efficiency activities undertaken by 89 groups in the UK, engaging and helping nearly 46,000 people, and saving consumers nearly £3 million. We’re working with four fantastic organisations here in Essex. This is just the start of what's possible and lots more can be done.”
Our panel looked at the question of growing the number of community retrofit schemes in Essex. Russell Smith, Managing Director at Parity Projects, said the key was getting people talking about energy. “Local community groups are extremely powerful, useful and trusted. Mobilising those guys is the secret sauce.”
One possible way of doing this would be getting more householders taking DIY energy efficiency measures. Jo Alsop, Founder of the Heating Hub provided some examples. “One of the biggest DIY energy-saving tweaks is to reduce the heating flow temperature from 80°C to 60°C or lower if possible. A recent report found that this could save 6-8% on fuel bills. It’s simple and safe to do yourself on combi boilers and you can access resources like a how-to video on our website.”
“The next step entails tailored advice, which includes homes with a hot water cylinder. In nearly all households it will be possible to reduce energy use further by optimising the boiler set up, fitting the right heating controls, setting the right heating temperature regime, optimising the radiators, and using the right heating engineer to bring it all together.”
Weather compensation controls and smart controls, said Dominic Hills, projects manager at Stelrad Radiators, could be a nice complementary way of improving the tangibility of energy as a concept to residents. “They are reliable. There are smart controls, TPI controls, which will actually measure and work out when to actually turn off and on, reducing flames on boilers. Like Joe says, there’s lots of tricks and things you can look at. And if you look at DEC some time ago, 8.5 million homes don’t even have a thermostat. We’ve got a big challenge. Building regs now say Thermostatic Radiator Valves need to be fitted. 6m homes still don’t have TRVs. There’s lots of smart controls that can work alongside weather compensation controls.”